Battery packs are the powerhouse behind countless electronic devices, from electric vehicles to portable gadgets. But what ensures their reliability, safety, and long lifespan? The secret lies in a meticulous manufacturing process comprising several stages, each critical to the final product’s quality.
Here’s a detailed look into the 9 essential steps involved in crafting a high-quality battery pack.
Step 1: Raw Material Selection
The foundation of any battery pack is its raw materials.
High-quality lithium-ion cells, connectors, and Battery Management System (BMS) components are essential for ensuring the pack’s performance, safety, and longevity.
The selection process involves sourcing materials that meet stringent specifications, including energy density, thermal stability, and conductivity. Using substandard materials can lead to poor performance, shorter battery life, and potential safety hazards, making this step crucial in the manufacturing process.
- At Tritek, we exclusively select Tier-1 battery cells and conduct both in-house and third-party cell tests to ensure the highest quality.
- Our connectors are designed to withstand over 10,000 plug-and-unplug cycles, ensuring durability and reliability.
- Additionally, we develop and manufacture our own BMS in-house, allowing us to maintain strict control over its quality and functionality.

Step 2: Cell Sorting and Matching
Once the raw materials are selected, the next step is cell sorting and matching.
Lithium-ion cells vary slightly in capacity, voltage, and internal resistance, even within the same production batch. To ensure balanced performance and longevity, cells must be carefully sorted and matched.
This involves testing each cell and grouping them according to their characteristics. Matching cells with similar properties ensures that they charge and discharge uniformly, preventing imbalances that could reduce the battery pack’s overall efficiency and lifespan.
Here we take our TP6068 battery pack as a sample, the cell sorting standard is:
- Battery cells are from the same batch
- The voltage difference between battery cells is less than 5 mV, and the internal resistance is less than 2 mΩ

Step 3: Battery Management System (BMS) Integration
The Battery Management System (BMS) is the brain of the battery pack. It monitors and controls the pack’s performance, ensuring safety and efficiency.
During the BMS integration process, sensors are connected to monitor parameters such as voltage, temperature, and current. The wiring is then configured to allow the BMS to manage the charging and discharging cycles effectively. Finally, the BMS functionalities are tested to ensure that it can protect the battery pack from overcharging, overheating, and other potential risks.
Step 4: Cell Module Assembly
With the BMS integrated, the next step is to assemble the cells into modules.
A module is a group of individual cells connected in a specific configuration to achieve the desired voltage and capacity. This process requires precision, as the cells need to be securely connected—often through welding or soldering—to form stable modules.

The integrity of these connections is vital, as any weak point could lead to malfunctions or safety issues. The completed modules are then ready to be assembled into the final battery pack.
Tritek uses resistance welding of battery module:
- Automatic welding machine
- Each weld point must have a tensile strength >156 N
- A qualified weld point must retain more than 70% of its material after a tensile test
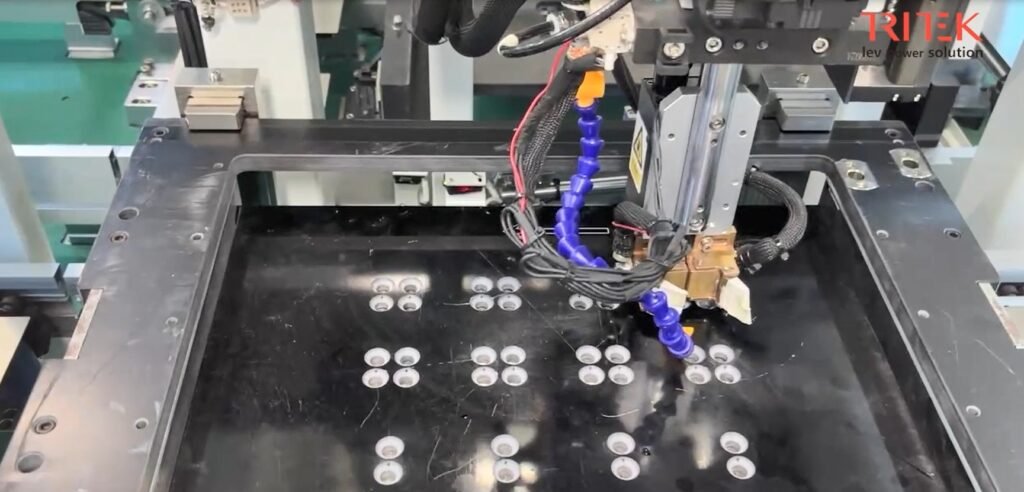
Step 5: Pack Assembly
The pack assembly process involves arranging the modules into the final configuration of the battery pack.
The connections between modules are secured to ensure stable electrical flow, and the entire structure is reinforced for durability.
This step also involves ensuring that the battery pack is designed to fit within the specific dimensions required for its application, whether it’s for an electric vehicle, a portable device, or industrial equipment.
Step 6: Enclosure and Structural Design
Once the battery pack’s internal components are assembled, the next step is to design and construct its outer enclosure.
The enclosure serves several critical functions: it protects the battery pack from physical damage, facilitates heat dissipation, and ensures the pack is compact and lightweight. Materials used for the enclosure are carefully selected to balance strength and weight, while the design is optimized to enhance the battery pack’s overall performance.
The final structure must be robust enough to withstand external forces and environmental conditions while remaining as compact as possible.
At Tritek, we usually use Aluminum as our enclosure material due to its combination of strength, heat dissipation, corrosion resistance, durability, recyclability, and design versatility.
Step 7: Encapsulation and Sealing
To further protect the battery pack, the encapsulation and sealing process is employed.
Encapsulation involves surrounding the battery pack with a protective layer to shield it from environmental factors such as moisture, dust, and mechanical shock. The sealing process ensures that the battery pack is airtight, preventing any external contaminants from entering and compromising its performance.

This step is crucial for ensuring the battery pack’s reliability and safety, especially in harsh operating conditions.
Most of Tritek’s battery packs are IP67 which can stand in various environments.
Step 8: Safety Testing and Quality Control
Safety testing and quality control are integral parts of the battery pack manufacturing process.
Before a battery pack is approved for use, it undergoes a series of rigorous tests to ensure it meets safety and performance standards. These tests include short-circuit testing, thermal stability assessments, vibration tests, and impact tests.
Each battery pack is evaluated against international standards, such as CE, FCC, UL2271, IEC62133, and EN15194, to ensure it complies with the necessary regulations. Quality control measures are also implemented at every stage of production to identify and rectify any defects or inconsistencies.
At Tritek, our battery packs are certified with UL2271, IEC 62133, EN 15194, EN 50604, etc.
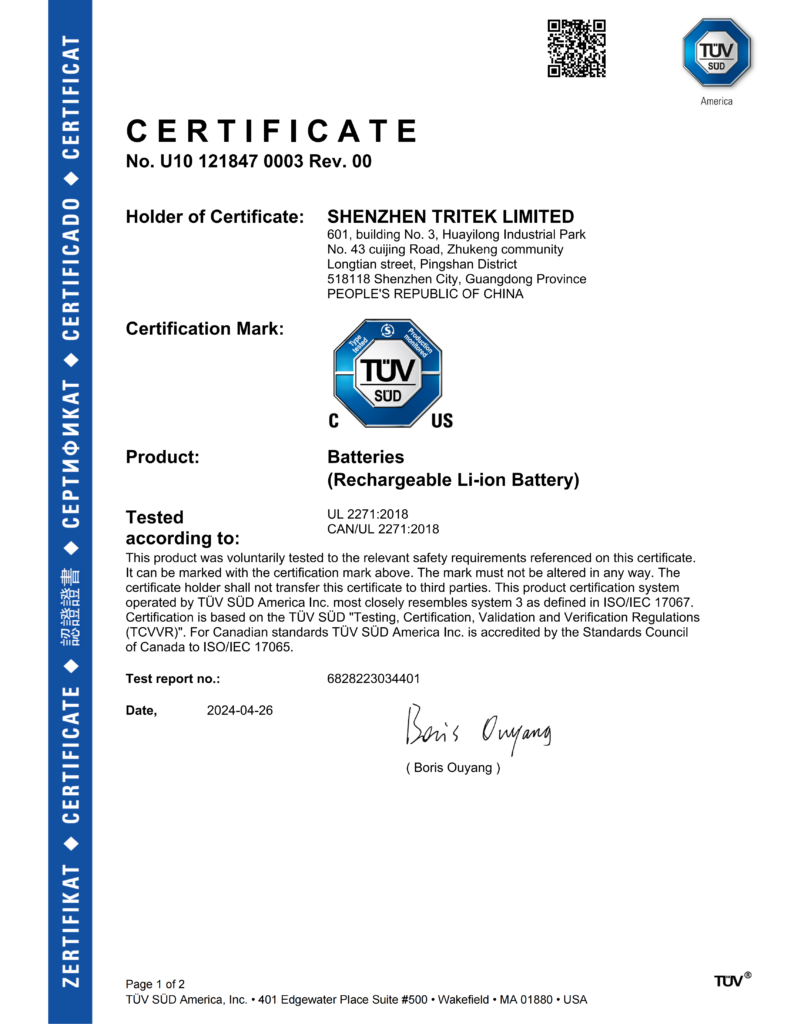
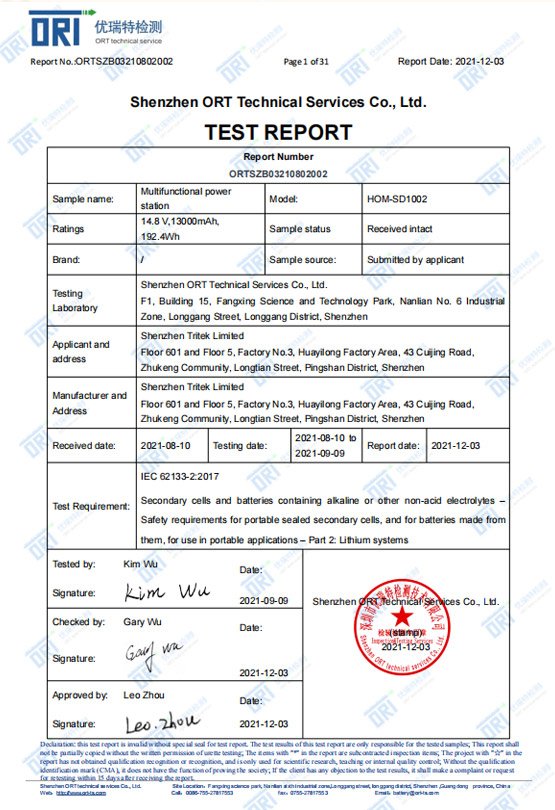
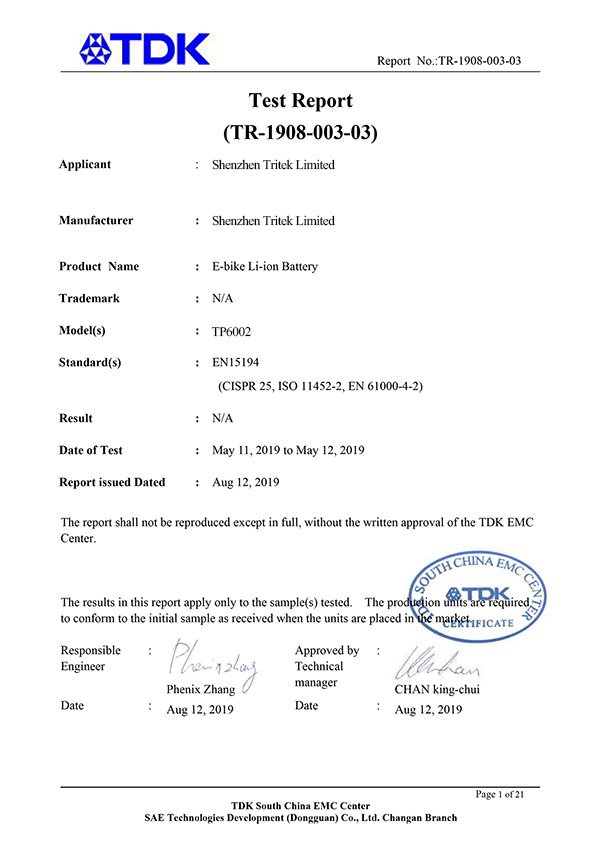
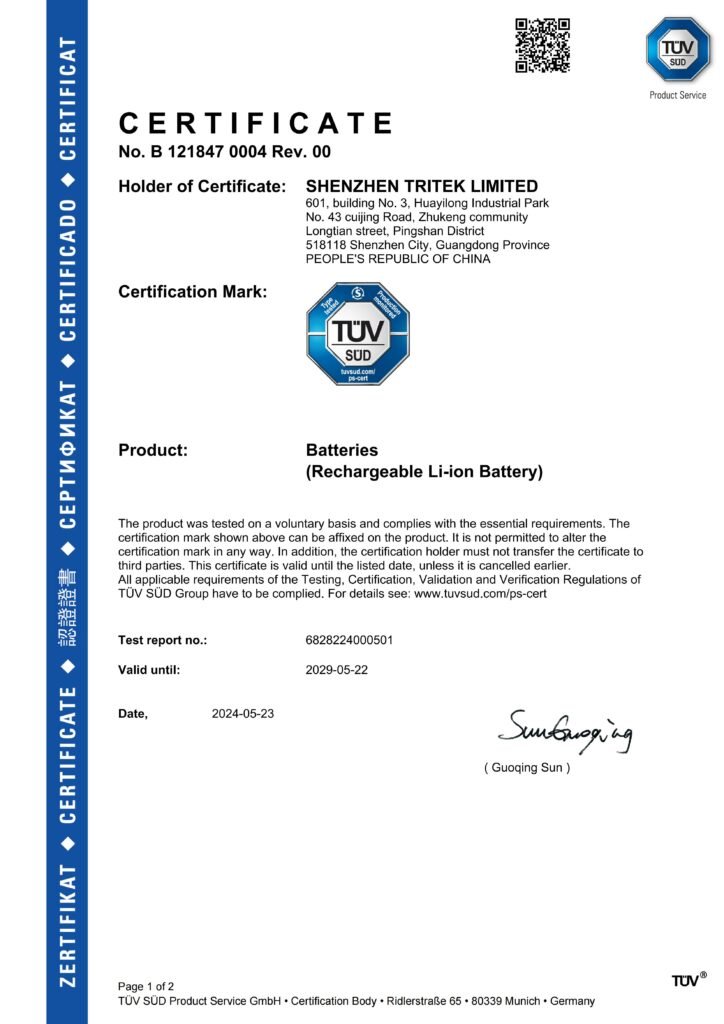
Step 9: Final Inspection and Testing
The final step in the manufacturing process is the final inspection and testing.
During this stage, the battery pack undergoes a comprehensive inspection to verify that all components are correctly assembled and that the pack meets all design specifications. Performance tests, such as capacity tests and cycle tests, are conducted to confirm that the battery pack functions as expected.
Only after passing these rigorous inspections and tests is the battery pack cleared for distribution, ensuring that it is safe, reliable, and ready for use.
Tritek will conduct communication tests, function tests, EOL(End-of-Line) tests, etc for the final product.
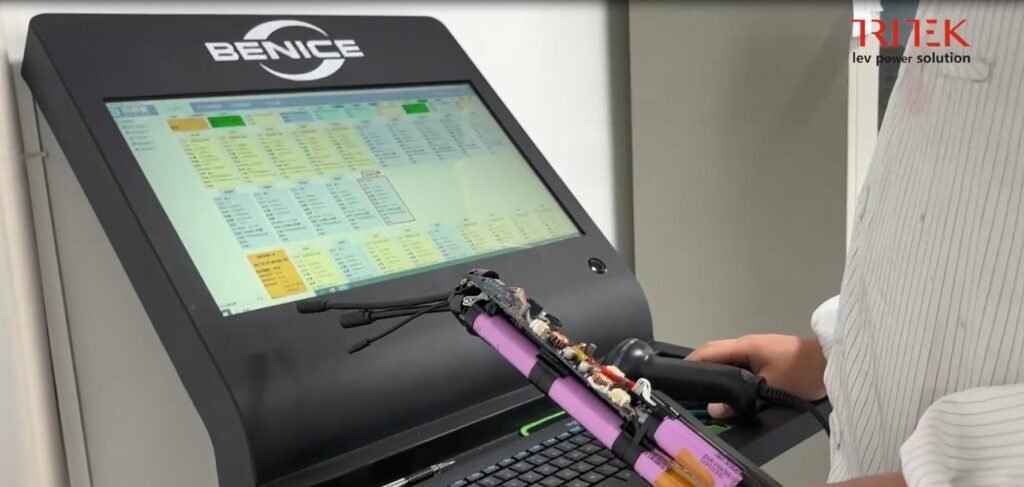
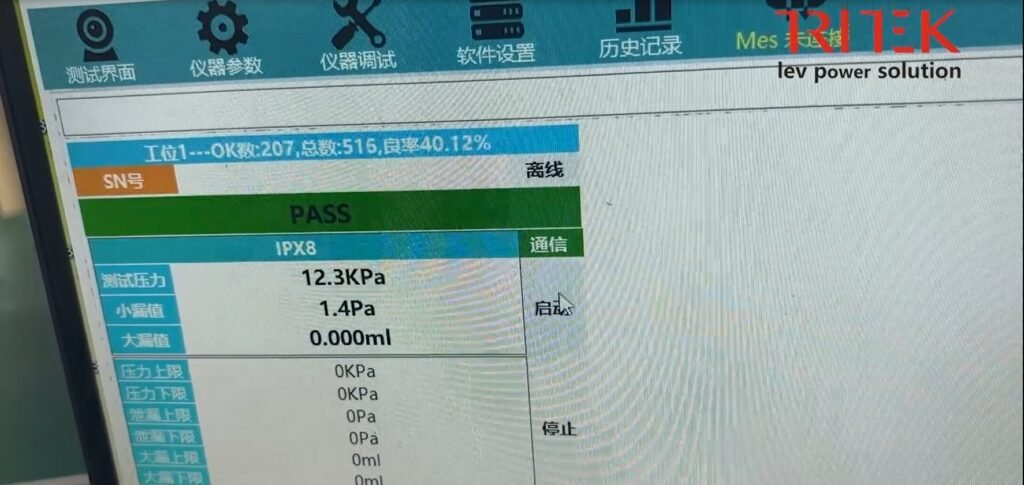
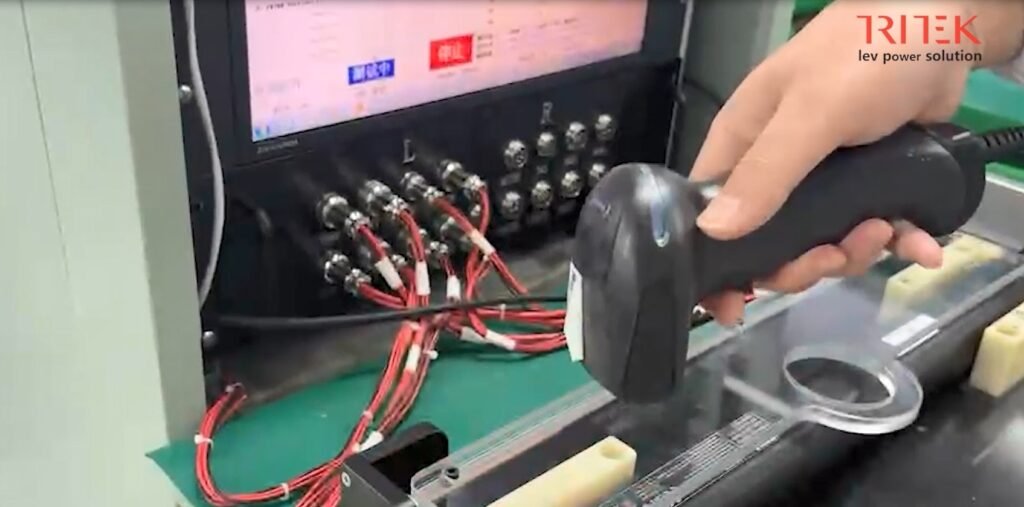
Conclusion
Manufacturing a high-quality battery pack is a complex process that requires precision, expertise, and strict quality control. From selecting the right materials to final inspection and testing, each step plays a critical role in ensuring the battery pack’s performance, safety, and longevity.
Understanding these nine essential steps provides valuable insight into the meticulous process behind the battery packs that power our modern world.
For more detail information, you can visit our video on Tritek’s Battery Pack Manufacturing Process.
Curious to learn more about how battery packs are made? Visit our Battery Pack Manufacturing Process page, which includes a detailed video.
Read More: